If you ever work in the field of medical, you are aware of how crucial accuracy is during surgical procedures. Custom surgical robot parts are now essential for improving the precision and effectiveness of these treatments with modern technological breakthroughs. As these parts involve in life changing surgeries so they need to highly precise and adaptive with excellent functionality. Multiaxis CNC machining is the key to attain this precision, the precision machining techniques offers faster lead times, cost savings, versatility, and scalability.
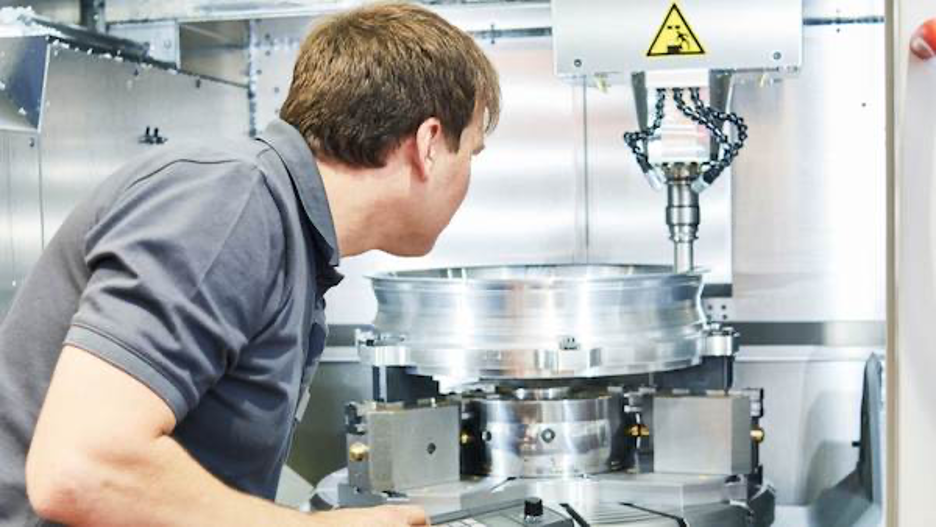
Further in this article we will figure how the CNC machining and technology advancement helps us in creating components that can drive innovation in the field of medical robotics.
Consistent Precision and Quality Control
The Most significant benefit of CNC machining for custom surgical robot parts is its consistent accuracy. The modern advanced multi-axis CNC machining process follows precise programming instructions, which avoids any variability that occurs in manual machining. Human error is completely eliminated even in high complex and intricate parts, guaranteeing constant precision in every part that is produced.
It is a fact that machining surgical robots demand micron level of precision and accuracy, and this precision is necessary as it ensures seamless integration of parts and avoid any malfunction that can occur due to bad manufacturing. The joint and actuator mechanism in surgical robots must be designed so that they can meet the kinematics needs and 360 degrees rotation sustainability for seamless articulation with in the robot’s framework. It will definitely help in increasing the reliability and functionality of the surgical robots.
In the medical field, dependability and regularity are very important. It is important that custom surgery robot parts meet strict quality standards to make sure that operations are safe and effective. With CNC cutting, you have complete control over the whole making process. This lets you make exact copies of parts with few changes.
Precision monitoring and correction made possible by computer numerical control (CNC) machining using CAD/CAM software guarantees the high quality of surgical robot parts throughout manufacture. When it comes to medical equipment, this degree of control is absolutely necessary to ensure the safety and dependability of the components.
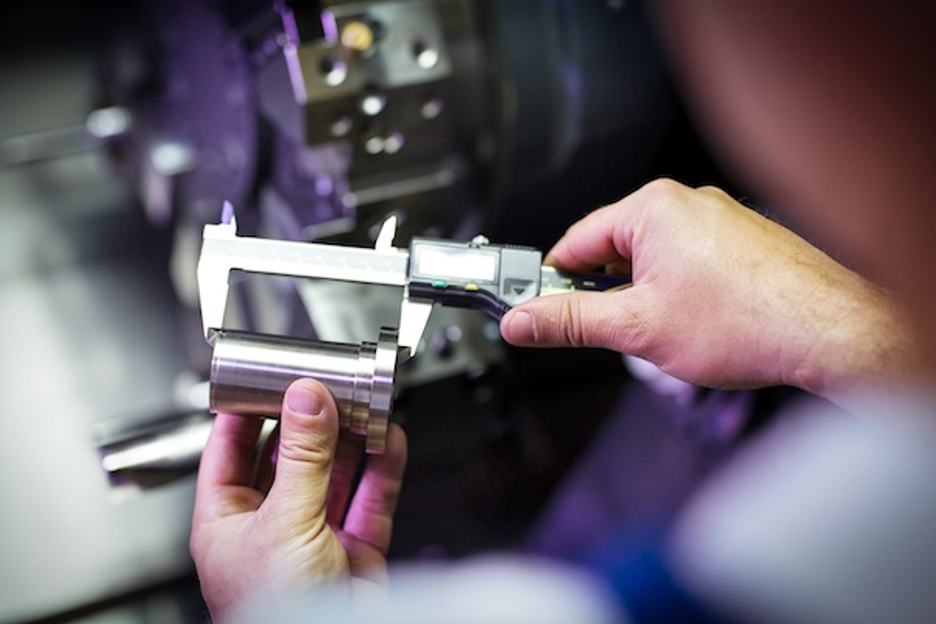
Versatility and Adaptability
The versatility and adaptability of CNC machines enable the engineers to explore new designs and materials, this will ultimately lead to the development of more advanced and efficient surgical robotic systems. The multi axis CNC machinery have the ability to adapt the technology changes which occur rapidly in advance surgical robots, as the medical field is evolving rapidly during this decade, to meet up this pace, engineers are able to design complex structures and random design changes and alterations with these multi axis’s machines.
Moreover, the CNC machining technology shows remarkable efficiency in seamlessly transitioning between different machining tasks like milling, boring and turning operations so that it ensures unparalleled adaptability in the production process. it is evident in the manufacturing of robotic joint components which require intricate milling operations for nuanced surfaces, precise turning for complex designed contours, and specific drilling for attachment points with the kinematically designed frame work.
In traditional machining operations, engineers need to change machines for each task, which consumes a lot of time of engineers and machinists specifically in the customization process. However, CNC machines save a lot of lead time in manufacturing. In short, the integration of CNC machining in customization and batch production will likely continue to play a pivotal role in shaping the future of medical robotics.
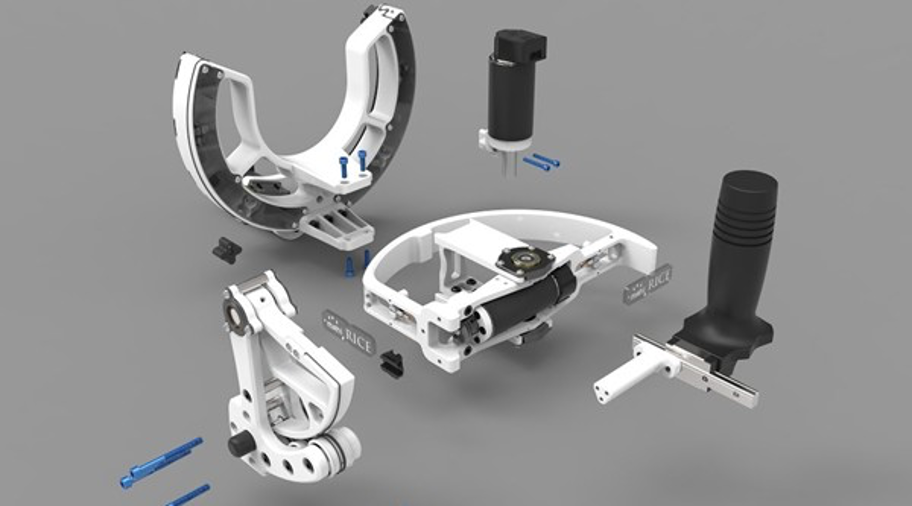
Versatility and Adaptability
In the realm of surgical robots, the customization is the most important paramount as for each patient the requirements are different as per their body anatomy. To achieve this level of customization CNC machining leads as the ideal manufacturing solution. The diverse surgical scenarios can only be addressed through the capability of CNC machining precise programming.
For instance, the robotic end-effector which is used for neurosurgical needs. For neurosurgical operation, the complexity of treating the patient needs delicate tissue manipulation or precise incisions. CNC machining practices are able to achieve these types of customized demand for the end-effectors. The second most important thing come in designing customize products is the use of desired material in manufacturing. Here again CNC machining with its divers machining ability allows the engineers to process diverse materials ranging from titanium, cast iron to medical-grade plastics.
But this type of customization is not only limited to the end effector only, CNC customization is almost implemented on every part of the surgical robots. If we talk about joint components, sensor housings, actuators or actuator or vision enhancement. the customization ensures that all the parts are perfectly align not only for a single product but for each customized production.
Faster Lead Times
Time is often of the essence in the medical industry. Custom surgical robot parts may be made rapidly and effectively with CNC machining. With CNC machines, production periods are faster than with traditional manufacturing techniques because of their automated nature.
Cutting-edge computer numerical control (CNC) machinery streamlines the manufacturing of surgical robot brackets and connections, allowing medical device companies to meet the ever-changing demands of the industry with lightning speed.
Cost Saving
Cost-effectiveness is equally as important in the medical industry as accuracy and productivity. Cost savings are possible with CNC machining in a number of manufacturing process areas. First off, the likelihood of expensive errors is much decreased when human error is eliminated. Second, the continuous operation of CNC machines maximizes production time and lowers labor expenses. Last but not least, the wide range of materials that CNC machines can work with minimizes material waste, which further cuts costs.
Conclusion
With different benefits that have advanced in the space of surgical advanced mechanics innovation, CNC machining has completely changed the way that adjusted cautious robot parts are made. Because of CNC machining’s precision and versatile features, experts could execute diverse strategies with greater efficiency and precision. Besides, dependable execution and solid results are guaranteed by the materials’ adaptability and extreme quality control technique.